System Sensor 2112 24AT Manual
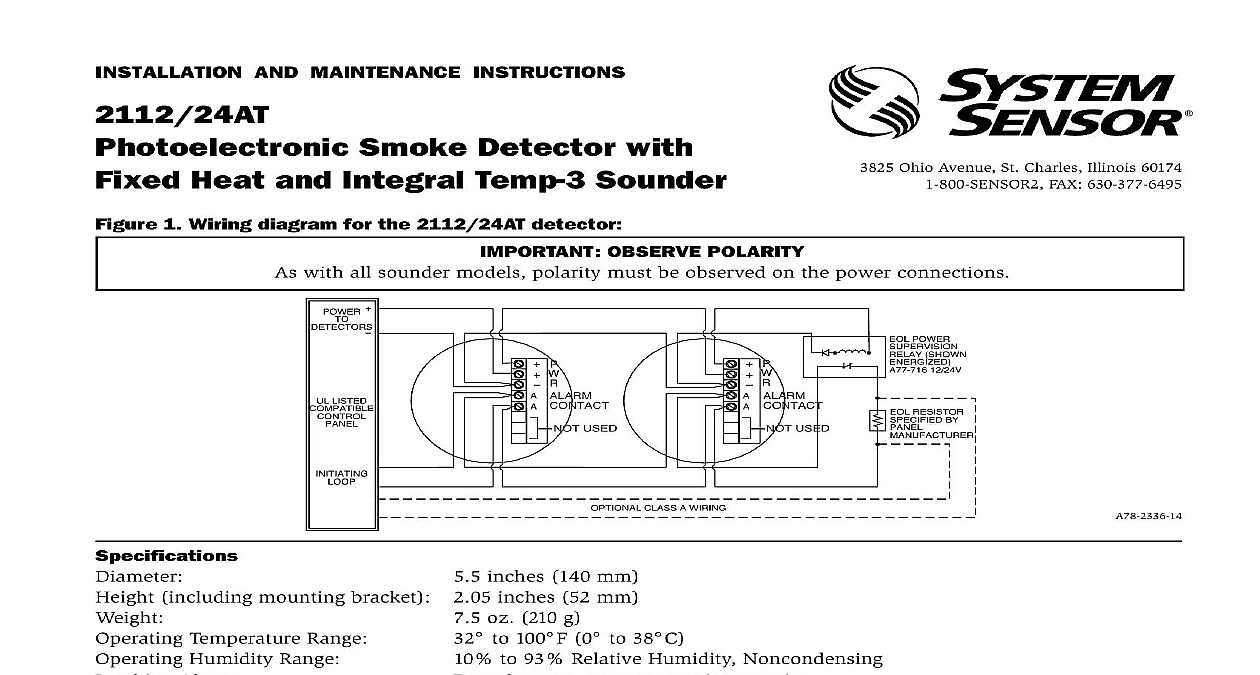
File Preview
Click below to download for free
Click below to download for free
File Data
Name | system-sensor-2112-24at-manual-3420179685.pdf |
---|---|
Type | |
Size | 666.69 KB |
Downloads |
Text Preview
INSTALLATION AND MAINTENANCE INSTRUCTIONS Smoke Detector with Heat and Integral Temp 3 Sounder 1 Wiring diagram for the 2112 24AT detector 3825 Ohio Avenue St Charles Illinois 60174 FAX 630 377 6495 with all sounder models polarity must be observed on the power connections OBSERVE POLARITY LISTED USED USED POWER SHOWN 12 24V RESISTOR BY CLASS A WIRING inches 140 mm inches 52 mm oz 210 g to 100 F 0 to 38 C to 93 Relative Humidity Noncondensing by momentary power interruption dBA minimum when in alarm or with supply polarity reversed Fixed Temperature Electronic Thermistor or 24 VDC VDC VDC of nom Voltage peak to peak maximum mA typical 60 mA max at 12V mA typical 65 mA max at 24V VDC minimum second maximum seconds maximum after 60 sec reset 12 24 VDC including mounting bracket Temperature Range Humidity Range Alarm Signal Sensor Ratings Voltage nominal Ripple Voltage Current Current Voltage Time Time Relay Initiation Rating Resistive Load Considerations 30 VDC to the built in temporal pattern use this detector only with a non coded supply Installing thoroughly read the System Sensor manual I56 407 for Proper Use of System Smoke Detectors which pro detailed information on detector spacing placement wiring and special applications Copies of this are available at no charge from System Sensor This manual shall be left with the owner user of equipment This detector must be tested and maintained NFPA 72 requirements The detector should be at least once a year 2 Surface mounting of 2112 24AT smoke on 31 2 inch and 4 inch octagonal box the LED stops blinking the unit should be removed for and inspection Description 2112 24AT is a 4 wire photoelectronic smoke detec that uses a state of the art optical sensing chamber detector also provides restorable 135 fixed tempera heat detection The unit has a heat detection unit that integrated with the photoelectronic sensor addition a piezoelectric horn in each detector produces interrupted 85 dBA tone when the individual detector or when the supply voltage polarity is reversed In order for all detectors on a loop to sound when panel alarms the panel must reverse the supply voltage to that loop upon alarm For panels that do not re the polarity during alarm a reversing relay such as Sensor RR 2 must be used The RR 2 is designed allow all the detectors in the same loop to sound when of the detectors goes into alarm Some panels may re the use of programmable outputs Refer to System literature for further information on the RR 2 of these detectors is simplified by the use of a bracket and a plug in screw terminal block that be prewired to the system allowing the detector to be installed or removed for cleaning The detector can be tested in place using the MOD400R Test LED on the detector provides a local visual indication of detector status If power is applied to the detector and is functioning normally in standby within the listed sensi range the status LED blinks every ten seconds The also latches on in alarm 3 2112 24AT smoke detector mounting bracket 2112 24AT detector is supplied with a mounting that permits the detector to be mounted To a single gang box or Directly to a 3 1 2 inch or 4 inch octagonal box or To a 4 inch square electrical box by using a plaster ring Directly to the ceiling using drywall anchors if permit by local codes and or the authority having jurisdic Feature detector includes a tamper resistant feature that pre its removal from the bracket without the use of a tool make the detector tamper resistant remove the smaller by breaking it at the scribed line on the tamper resistant on the detector mounting bracket see Figure 3 then the detector To remove the detector from the bracket it has been made tamper resistant use a small screw to depress the tamper resistant tab located in the on the mounting bracket and turn the detector coun Installation Guidelines wiring must be installed in compliance with the Na Electrical Code applicable local codes and any spe requirements of the local authority having jurisdiction wire gauges should be used The conductors used to smoke detectors to control panels and accessory should be color coded to reduce the likelihood of errors Improper connections can prevent a system responding properly in the event of a fire screw terminal block accepts 14 22 gauge wire For system performance all wiring should be installed in grounded conduit Do not mix fire system wiring the same conduit as any other electrical wiring Twisted may be used to provide additional protection against interference detectors and alarm system control panels have for allowable loop resistance Consult the panel specifications for the total loop resistance al for the control panel being used before wiring the loops SLOT TAB TO DETECTOR RESISTANT TAB CUT OFF SMALL TAB TO ACTIVATE TAMPER RESIST FEATURE power from the control unit or initiating device cir before installing detectors Smoke Entry Test connections are made by stripping about 1 4 inch of from the end of the feed wire inserting the wire the appropriate terminal and tightening the screw to the wire in place Wire the plug in screw terminal block per Figure 1 and the terminal block into the detector Align the arrows on the detector with the arrows on the Turn the detector clockwise in the mounting bracket un bracket it clicks into place After all detectors have been installed apply power to control unit or initiating device circuits Test the detector as described in TESTING Reset the detector at the system control panel Notify the proper authorities the system is in operation covers are an effective way to limit the entry of dust smoke detector sensing chambers However they may completely prevent airborne dust particles from enter the detector Therefore System Sensor recommends the of detectors before beginning construction or other producing activity Be sure to remove dust covers from sensors that were left in place during construction as of returning the system to service Before testing notify the proper authorities that smoke detector system is undergoing mainte and will be temporarily out of service Dis the zone or system undergoing maintenance prevent unwanted alarms Press and hold the recessed test switch with a 0.18 maximum diameter tool such as an allen wrench small screwdriver The detector LED should light within 5 seconds Test Module System Sensor Model No MOD400R MOD400R test module can be used with a DMM or voltmeter to check the detector sensitivity as de in the test module manual a smoldering punk stick or cotton wick at the side the detector and gently blow smoke through the de until the unit alarms Direct Heat Method Hair dryer of 1000 1500 watts the heat toward either of the side thermistors the heat source about 12 inches from the detector order to avoid damage to the plastic The detector will only after it has had sufficient time to cool and the source has been momentarily interrupted smoke and heat detection testing are recommended verifying system protection capability detector that fails to activate with any of the above tests first be cleaned as outlined in MAINTENANCE If detector still fails to activate return it for repair the proper authorities the system is back in Before removing the detector notify the proper au that the smoke detector system is under maintenance and will be temporarily out of Disable the zone o