System Sensor FAAST Modbus Schema 2
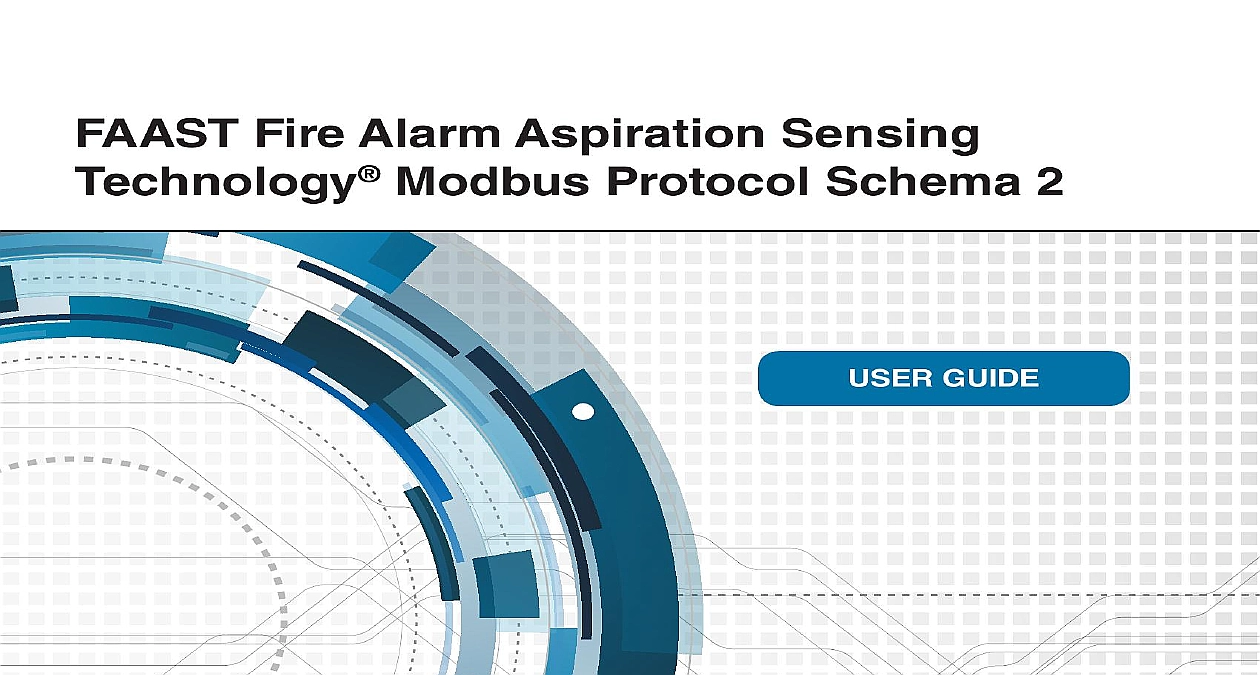
File Preview
Click below to download for free
Click below to download for free
File Data
Name | system-sensor-faast-modbus-schema-2-8620743591.pdf |
---|---|
Type | |
Size | 1.54 MB |
Downloads |
Text Preview
FAAST Fire Alarm Aspiration Sensing Modbus Protocol Schema 2 GUIDE of Contents Description 3 Interface 3 Interface 3 Registers 3 Format 3 Sensor Status and Control Operations 4 Administrator Password 4 Identifier 4 Read 4 Output and Operating Mode Control 5 Configuration 5 Time 6 Smoke Reference 6 Logs 7 Log Read 7 Log Read 7 Log Read 7 Configuration 8 Registers 8 Registers 9 Status 9 Status 11 Logs 13 Configuration 14 Configuration 15 Configuration 17 A Configurable options on FAAST 18 Alarm Configuration Variables 18 Device Configuration Variables 19 Table of Change Release for Review Modbus Slave ID Guide FAAST Fire Alarm Aspiration Sensing Technology Modbus Protocol Schema 2firealarmresources com Description FAAST Fire Alarm Aspiration Sensing Technology aspirating smoke detector is an advanced particulate detection system for use in early warning and very early warning fire detection applications FAAST draws air from the environment through holes in a pipe network and monitors for smoke particulates FAAST includes a local display which provides a clear of the devices status Smoke particulate level alarm level air flow and faults can all be discerned with a glance at the interface is also enabled by built in Modbus communications capabilities The Modbus Protocol utilizes the TCP server They physical is Ethernet is a communications protocol allowing for connectivity with several building management solutions Using Modbus a device can be monitored remotely and various device configuration actions and device interactions are facilitated NOTE WHILE Modbus CAN BE USED TO SET DEVICE CONFIGURATIONS THE DESIGN OF ANY NEW FAAST MUST BE VERIFIED USING PipeIQ TO ENSURE THAT SITE SPECIFIC REQUIREMENTS ARE MET IF Modbus IS USED MODIFY AN INSTALLED UNIT ANY CHANGES TO SENSITIVITY SETTING SHOULD ALSO BE VERIFIED IN PipeIQ TO CONTINUED SYSTEM PERFORMANCE Interface protocol stack is an application that runs over TCP The device requires a 10 or 100Mbps Ethernet connection to an existing network and a valid network configuration in order to enable Modbus Communications The FAAST device TCP server will listen Modbus protocol packets on Port 502 TCP ports allow Modbus e mail PipeIQ and web communications simultaneously Finally to transmit and receive data over the user requires a client that can generate Modbus packets over TCP Interface a client is connected through Port 502 the FAAST device will act as a Modbus TCP This section defines the format of in Modbus TCP registers More information about Modbus TCP can be obtained from www Modbus org entire Modbus map is related to a single device and the Slave ID parameter is unused by the FAAST device properly transfer data to and from the Modbus registers the following descriptions specify how data is organized when more than register is required to read or write a specific piece of data Registers registers for registers listed in Table 1 registers in Tables 2 to 8 Format Long Integer floating point 0xaabbccdd Reg1 0xaabb Reg2 0xccdd String Reg1 Reg2 IP Address a b c d Reg1 dc Reg2 ba MAC Address 0x aa bb cc dd ee ff Reg1 0xbbaa Reg2 0xddcc Reg3 0xffee Guide FAAST Fire Alarm Aspiration Sensing Technology Modbus Protocol Schema 2Rev Bfirealarmresources com Sensor Status and Control Operations Administrator Password Modbus Administrator Password grants the user the privilege of writing to the Holding Registers This password is the same as User Interface Button Lockout Code It is not readable through the Modbus Interface It is set to as the default The values range from 1111 to 9999 The user may change the password by performing a Device Configuration Change as described failure to gain administrator privileges due to a forgotten or lost password is a recoverable event by using the PipeIQ software to the device and updating the device configuration with a known password Modbus Slave Identifier is set in PipeIQ The device will respond to Modbus commands at the device configured Device The valid range is 1 247 Identifier Eclipse Flashscan CLIP The Device Identifier is set in PipieIQ T