System Sensor Successfully Deploying FAAST in Duct Applications
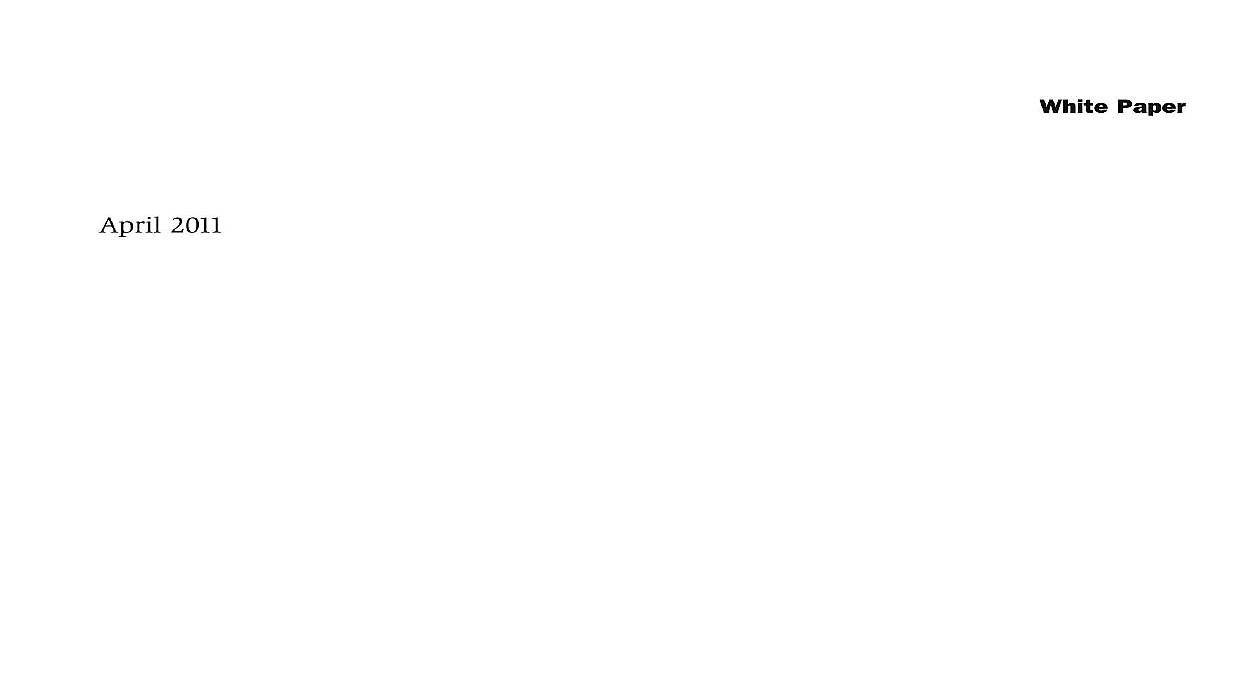
File Preview
Click below to download for free
Click below to download for free
File Data
Name | system-sensor-successfully-deploying-faast-in-duct-applications-4230859176.pdf |
---|---|
Type | |
Size | 849.36 KB |
Downloads |
Text Preview
April 2011 Paper Deploying Fire Alarm Aspiration Sensing Technology Duct Applications Deploying FAAST Fire Alarm Aspiration Sensing Technology In Duct Applications FAAST Fire Alarm Aspiration Sensing Technology 8100 smoke detector an extremely flexible combustion particulate sensor It is suitable for a of fire protection applications ranging from high sensitivity open air of data centers to HVAC duct protection of theaters The 8100 is the aspirating smoke detector ASD designed to specifically discriminate from smoke particulate Using its unique dual vision sensing technology detector is better able to discern threat from nuisance limiting false and keeping your facility operational 24 7 Sampling Not So Trivial of the many popular uses of ASDs is in air handling duct applications traditional duct smoke detectors ASDs usually offer higher sensitivity active sampling with the benefits of active sampling come additional challenges are required to monitor and maintain a minimum airflow volume operating inside ductwork this can present a significant test of the capabilities Not only will air speeds vary from duct to duct but air will often vary significantly within a duct These variable air speeds due to air handling units turning on and off or variable frequency drives provide more precise flow adjustments The consequences to an ASD variable air speeds can be as inconvenient as a flow fault or as dangerous a reduction in sensitivity Duct Detection order to mitigate flow faults while maintaining adequate sensitivity care be taken when using an ASD in a duct application System Sensor tested the FAAST 8100 in a number of duct configurations Analysis of results and industry best practices has lead System Sensor to make the throughout the remainder of this whitepaper Ducts ducts less than 3 feet wide the sampling pipe should be inserted into duct at a height equal to half of the duct height Figure 1 1 Diameter Duct Flow Pipe Pipe Sensor Advanced Ideas Advanced Solutions Deploying FAAST Fire Alarm Aspiration Sensing Technology In Duct Applications consult local fire for hole size and requirements 1 Sampling Pipe Hole Size Small Diameter Duct WIDTH in 300 mm in 500 mm in 700 mm in 900 mm OF SIZE PIPE FLOW RATE in 6.5 mm in 6.5 mm in 4.5 mm in 4 mm cfm 52.0 L min cfm 51.9 L min cfm 48.1 L min cfm 51.2 L min sampling pipe holes use Table 1 to drill evenly spaced holes into the pipe along the same line The hole drilling line should be marked permanent ink and should be visible from outside the duct Ducts ducts larger than 3 feet wide a branch configuration employing two pipes should be used One pipe should be inserted into the duct a height equal to 3 4 of the duct height The other pipe should be inserted the duct at a height equal to 1 4 of the duct height Figure 2 2 Diameter Duct Flow Pipe Pipe sampling pipe holes use Table 2 to drill evenly spaced holes into the pipe along the same line The hole drilling line should be marked permanent ink and should be visible from outside the duct 2 Sampling Pipe Hole Size Large Diameter Duct WIDTH ft 4 in 1 m ft 1.5 m ft 6 in 2 m OF SIZE PIPE FLOW RATE in 3.5 mm in 3 mm in 3 mm cfm 50.2 L min cfm 50.9 L min cfm 59.6 L min consult local fire for hole size and requirements Sensor Advanced Ideas Advanced Solutions Deploying FAAST Fire Alarm Aspiration Sensing Technology In Duct Applications Pipe exhaust pipe should be located approximately 18 inches downstream the sampling pipe s The exhaust pipe should be inserted into the at a height equal to 1 4 of the duct height exhaust pipe may be set up in two different configurations The first consists of a pipe of the same length as the sampling pipe with four inch holes Traditionally fitting the exhaust pipe with holes has been way to install ASDs in ducts This configuration promotes somewhat stability to the airflow passing through the detector with less overall volume as a tradeoff When employing this configuration System recommends orienting the exhaust holes directly away from the second option is a short pipe that protrudes 2 to 3 inches into the duct is not fitted with an end cap This is a simpler method and promotes overall airflow through the detector However this arrangement may more prone to faults caused by duct airflow fluctuations System Sensor trying this configuration first and reverting to the traditional if stabilizing the airflow pendulum proves difficult determining the proper number and sizes of sampling pipes and holes all pipe should be cut to the proper length and holes added FAAST 8100 should be mounted to a nearby adjacent location and pipe run to the duct a rule of thumb duct sampling pipes should be located a distance of at six duct widths from any disturbances to the duct airflow caused by bends or branch connections Holes should be cut into the ductwork the appropriate location in the manner described above all pieces assembled insert the sampling and exhaust pipes into the but do not seal or cement Using the line marked on the sampling orient the holes such that they are facing into the airflow and directed at approximately 45 degrees Sensor Advanced Ideas Advanced Solutions Deploying FAAST Fire Alarm Aspiration Sensing Technology In Duct Applications the System the air handling units off power up the 8100 and connect to it using PipeIQ software Using the PipeIQ set the desired configuration and reconfigure the device Upon receiving a new configuration 8100 will automatically power down and reset After a brief startup allow 5 minutes for the 8100 to adjust to the new pipe network 5 minutes have elapsed turn on the air handling units preferably at highest velocity Observe the behavior of the green airflow pendulum on front of the 8100 If the pendulum begins to swing to the left not enough is entering the aspirating detector Using the mark on the sampling pipe reference carefully adjust the sampling pipe so that the holes are facing more towards the oncoming airflow A few degrees of rotation may a significant impact After making the adjustment wait at least 20 to seconds for the airflow to stabilize and the pendulum to update the pendulum swings to the right too much air is entering the ASD the mark on the sampling pipe for reference carefully adjust the pipe so that that the holes are facing slightly more away from airflow After making the adjustment wait for the airflow to stabilize the pendulum to update Continue adjusting as necessary until the remains fixed directly in the middle position satisfied with the position of the sampling tube shut off the air units and observe the airflow pendulum It should remain at or near middle position Mark the angle of rotation on the duct and complete installation by sealing and securing the sampling tube as appropriate smoke testing as prescribed by the authority having jurisdiction aspirating smoke detectors inside ductwork requires planning and By following the recommendations in this document and carefully the angle of the sampling pipe you will be able to successfully install FAAST ASD in high velocity air ducts while minimizing the occurrence flow faults With the flow issue resolved facility operators will be able enjoy the superior dust rejection and numerous other innovations that the 8100 the new standard in Very Early Warning Fire Detection Sensor Advanced Ideas Advanced Solutions Deploying FAAST Fire Alarm Aspiration Sensing Technology In Duct Applications Sensor Advanced Ideas Advanced Solutions Deploying FAAST Fire Alarm Aspiration Sensing Technology In Duct Applications Sensor Advanced Ideas Advanced Solutions Deploying FAAST Fire Alarm Aspiration Sensing Technology In Duct Applications more inf